This cooperation is between a new fiber technology company in Vietnam established in 2014 and
Sitong boiler. Its an enterprise who is mainly engaged in the research and development, production, and sales of fiber fabrics, PU, PVC synthetic leather, and related products. As a production material for clothing, shoes, bags, etc., the company's fiber fabrics and synthetic leather products have good sales and high market demand, but are in short supply. In response to market demand, the company decided to expand its existing fiber fabric and synthetic leather product production line, eliminate outdated heating equipment on the production line, and introduce an 8 million kcal YLW series biomass fired thermal oil heater produced by
Sitong boiler to meet its heat source needs on the production line, and choose bark as boiler fuel. Bark is a renewable energy source and has a lower price compared to materials such as coal, oil, and natural gas. The price of biomass fuel is relatively less affected by market changes, which can help the enterprises save a certain amount of raw material costs. In addition, the use of biomass fuels does not produce harmful gases such as greenhouse gases and acid rain, and has low emissions of nitrogen oxides and particulate matter. It has a relatively small impact on air quality and can reduce environmental pollution.
Sitong boiler's 8 million kcal YLW series biomass thermal oil boiler is a horizontal chain grate assembled boiler with the chain grate and boiler body shipped separately. It only need to be connected to pipelines, valves, control lines, oil and electricity can be connected to put them into operation after the boiler components are transported to the factory. The installation cycle is short, which can save a lot of installation costs for enterprises. In addition,
Sitong boiler's YLW series biomass fired thermal oil heater adopts a square tube structure, which optimizes the radiation heating surface to ensure the full combustion of the biomass fuel. The inner side of the boiler is built with high-quality refractory bricks, the external side is concave convex panel, and high-quality perlite is used in the middle to control the temperature of the furnace below 50 ℃, which can effectively reduce the heat loss of the boiler. In order to reduce heat loss,
Sitong boiler also recovers and utilizes the waste heat from high-temperature flue gas through various energy-saving devices, thereby improving the overall thermal efficiency of the boiler and achieving the goal of energy conservation and consumption reduction. The designers of
Sitong boiler have also installed energy-saving devices at the rear of the boiler, which recycle and utilize the waste heat from high-temperature flue gas to achieve energy conservation and reduce consumption that help the enterprise achieve production and efficiency.
More information on LinkedIn:
https://www.linkedin.com/feed/update/urn:li:activity:7275779419670028288Delivery video on YouTube:
https://www.youtube.com/watch?v=cP0Dmfhtg0I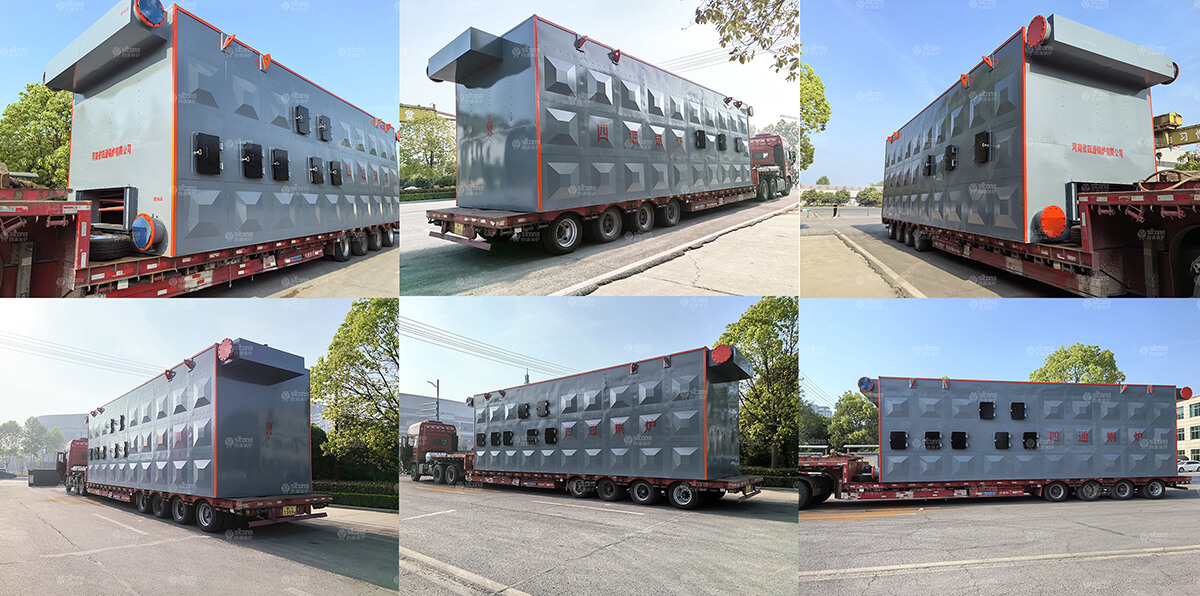