A pet food factory in Thailand was established in 2015, mainly engaged in pet food processing and sales. Due to production needs, the factory plans to add a 15 ton biomass fired steam boiler to provide stable heat energy for the production line, which is used for food drying and sterilization processes. It has also decided to use palm shells as boiler fuel. Pet food processing is relatively refined, and generally the newly purchased raw materials need to be monitored before use. Grinding and mixing of raw materials, followed by puffing, is a key step in the pet food manufacturing process that requires the use of steam heating and pressure provided by a steam boiler. Under the action of high temperature and pressure, the raw materials are fully mixed and matured, and the starch is heat treated to improve its digestibility, reducing the phenomenon of pet diarrhea or bloating caused by undigested starch in the pet intestine of pet food products. Then, production is completed through a series of processes such as pressing particle shapes, product quality control, drying particles, vacuum spraying, cooling, packaging, etc. The temperature control requirements during the production process are very strict.
The DZL series biomass fired steam boiler from
Sitong boiler arranges the furnace arch, furnace wall, and furnace heating surface reasonably through numerical simulation based on the characteristics and combustion rate of various biomass fuels. Compared to traditional boilers, the DZL series biomass fired steam boiler has a larger furnace space and a very reasonable arrangement of secondary air to fully burn and effectively reduce NOX emissions. Configure a speed control box for it, which can adjust the speed reasonably based on the biomass combustion rate to ensure fuel burnout and achieve zero carbon dioxide emissions. The use of this biomass fired steam boiler from
Sitong boiler further solves the problem of ash accumulation in the convection area of the boiler. The flue gas enters the convection zone from the furnace outlet, and the return path in the flue gas directly settles to the bottom of the convection zone. Then, the accumulated ash is placed on the grate through a rotating ash discharge valve and pipe, achieving real-time ash discharge. The boiler has high thermal efficiency, sufficient combustion, and is not prone to dust accumulation, making it an excellent environmentally friendly boiler product. At present, the boiler has been successfully shipped with a compact structure and easy installation, which not only saves customers a lot of infrastructure investment, but also reduces operating costs and pollution emissions due to its efficient and low emission characteristics.
More information on Facebook:
More information on LinkedIn:
Delivery video on Youtube:
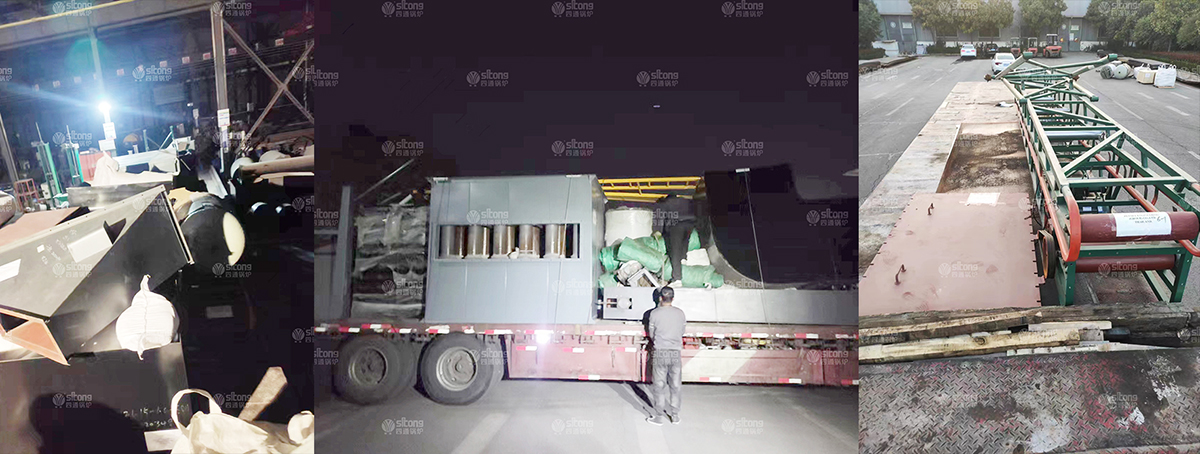